Thermal Stability & Wear Resistance: Ceramic Spray Nozzles are trusted for their durability and longevity
The use of ceramics in spray nozzles provides enhanced durability, chemical resistance, thermal stability, precise spraying capabilities, resistance to clogging, and electrical insulation
Ceramic materials are commonly used in the manufacturing of spray nozzles. Ceramic spray nozzles offer several advantages over other materials, making them suitable for a wide range of applications. Here are some key points about ceramic spray nozzles:
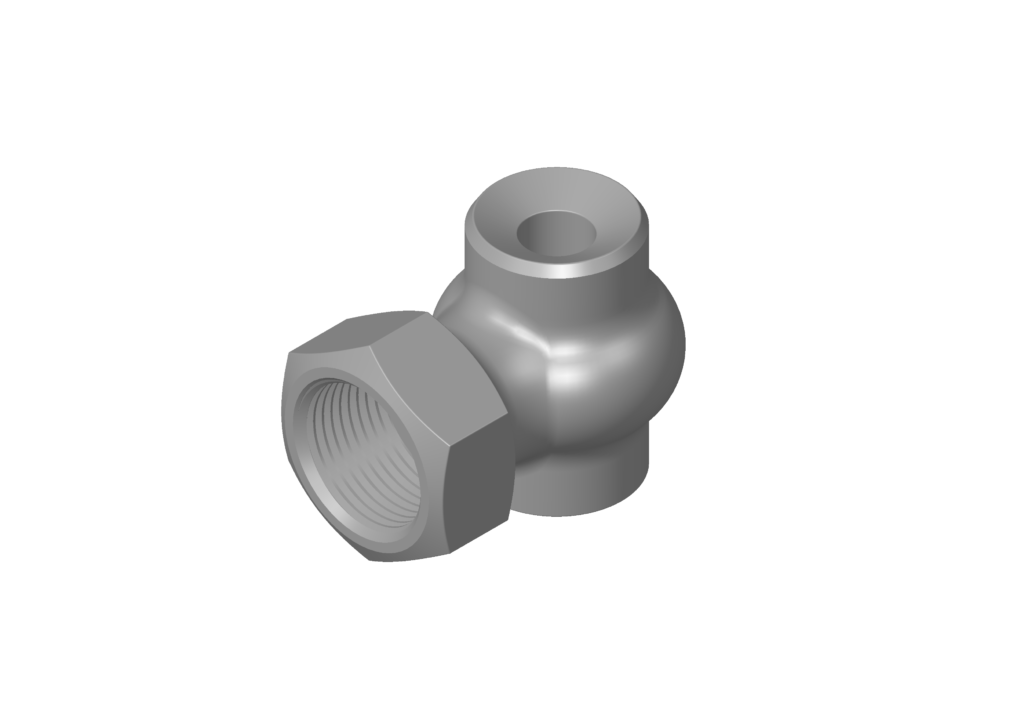
Ceramics are known for their exceptional hardness and wear resistance. When used as spray nozzles, ceramics can withstand abrasive materials and harsh operating conditions without significant wear or degradation. This durability allows for prolonged nozzle lifespan and consistent performance.
Ceramic spray nozzles exhibit excellent resistance to various chemicals, acids, and alkalis. This makes them suitable for applications where the nozzle comes into contact with corrosive substances, such as in chemical processing, wastewater treatment, or agricultural spraying.
Ceramics can withstand high temperatures without deformation or deterioration. This property is particularly advantageous in applications that involve high-temperature fluids or thermal processes, including metal processing, heat treatment, or combustion systems.
Ceramic spray nozzles can be manufactured with high precision, resulting in controlled and efficient spray patterns. The smooth surface finish of ceramics helps in achieving uniform droplet distribution and consistent spray coverage, leading to improved process efficiency and reduced material wastage.
The smooth, non-porous surface of ceramic nozzles minimizes clogging or blockage due to sediment or debris present in the fluid being sprayed. This is particularly beneficial in applications such as agricultural spraying, where nozzle clogging can adversely affect spray distribution.
Ceramics are electrically insulating materials, which is advantageous in applications where electrical conductivity needs to be avoided. For example, in electrostatic spraying or coating processes, ceramic nozzles prevent the buildup of static electricity and potential hazards.
Ceramic spray nozzles find applications in various industries, including agriculture, automotive, chemical processing, metal fabrication, food and beverage, and more. They are used in processes such as spraying liquids, coatings, atomization, dust suppression, gas cooling, and surface cleaning. The unique properties of ceramics make them a reliable choice for spray nozzle applications that require durability, chemical resistance, precision, and thermal stability.