Exploring the Different Types of Pumps
Dive into the diverse world of pumps, from centrifugal and positive displacement to reciprocating and submersible varieties.
Centrifugal pumps are the most common type of pump used in various industries. They work on the principle of centrifugal force, where an impeller rotates to create a suction that draws fluid into the pump and then forces it out through the discharge outlet. Centrifugal pumps are efficient in moving large volumes of fluids, such as water, chemicals, and petroleum products. They are widely used in water supply and distribution, irrigation, HVAC systems, and wastewater treatment.
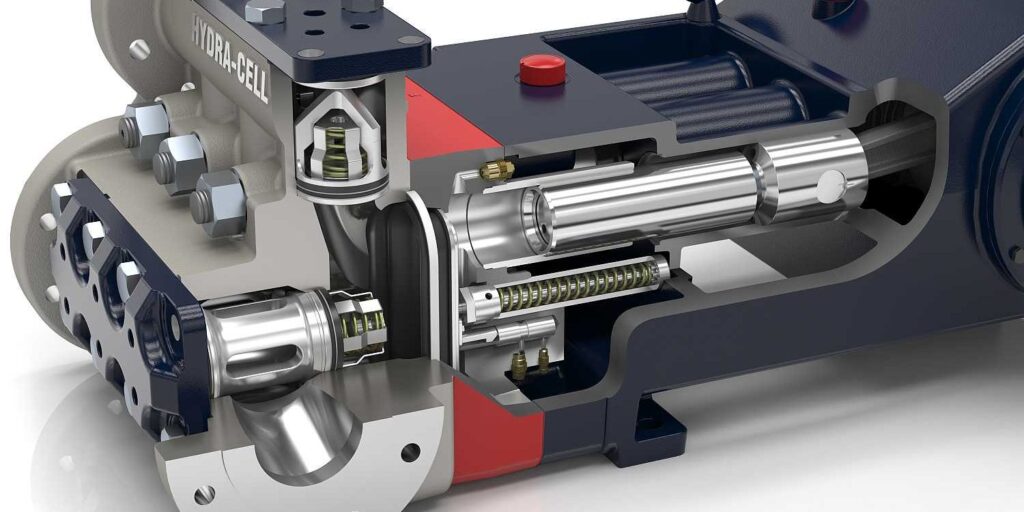
Positive displacement pumps operate by trapping a fixed volume of fluid and then forcing it into a discharge pipe. These pumps are suitable for handling viscous liquids, slurries, and liquids with variable flow rates. Positive displacement pumps are known for their ability to maintain a constant flow rate regardless of changes in pressure. Common types include: a. Piston Pumps: Piston pumps use reciprocating pistons or plungers to create pressure and move the fluid. They are commonly used in high-pressure applications such as hydraulic systems, car wash systems, and oil and gas industry. b. Gear Pumps: Gear pumps consist of meshing gears that create a pumping action by trapping and moving fluid between the gear teeth. They are often used for transferring lubricating oils, fuels, and other viscous fluids. c. Screw Pumps: Screw pumps, also known as progressive cavity pumps, use an Archimedean screw-shaped rotor to move fluid through the pump. They are suitable for handling thick and viscous liquids, sludge, and wastewater. d. Diaphragm Pumps: Diaphragm pumps utilize a flexible diaphragm that moves back and forth, creating pressure and moving the fluid. These pumps are ideal for handling corrosive or abrasive fluids as the diaphragm acts as a barrier between the fluid and pump components. Diaphragm pumps are commonly used in chemical processing, pharmaceuticals, and food industries.
Reciprocating pumps use a reciprocating motion of a piston or plunger to create pressure and move the fluid. They are known for their high-pressure capabilities and are often used in applications such as high-pressure cleaning, oil and gas industry, and hydraulic systems. Reciprocating pumps can be further categorized into: a. Plunger Pumps: Plunger pumps use a reciprocating plunger to move the fluid. They are capable of generating very high pressures and are commonly used in industries like oil and gas, pressure washing, and water jetting. b. Diaphragm Pumps: As mentioned earlier, diaphragm pumps use a flexible diaphragm to generate pressure and move the fluid. They are often preferred for applications that require handling hazardous or corrosive fluids.
Rotary pumps operate by the rotation of a rotor within a chamber to move the fluid. They are commonly used for pumping viscous liquids, oils, and fuels. Some types of rotary pumps include: a. Gear Pumps: Gear pumps, as mentioned earlier, use meshing gears to pump fluid. They are suitable for a wide range of viscosities and are commonly used in hydraulic systems, lubrication systems, and fuel transfer applications. b. Vane Pumps: Vane pumps utilize vanes mounted on a rotating rotor to create suction and move the fluid. They are suitable for low to medium viscosity fluids and are commonly used in automotive applications, power steering systems, and hydraulic systems. c. Screw Pumps: Screw pumps, as mentioned earlier, use an Archimedean screw-shaped rotor to pump fluid. They are suitable for handling highly viscous fluids, sludge, and wastewater.
Submersible pumps are designed to be fully submerged in the fluid they are pumping, typically water or wastewater. They have a hermetically sealed motor and are commonly used in applications such as drainage, sewage systems, deep well water extraction, and underwater mining operations.
Vacuum pumps are used to create or maintain a vacuum by removing gas molecules from a sealed chamber. They find applications in various industries, including manufacturing, laboratories, food processing, and electronics. Common types of vacuum pumps include: a. Rotary Vane Pumps: Rotary vane pumps use rotating vanes to create a vacuum by trapping and exhausting gas molecules. b. Liquid Ring Pumps: Liquid ring pumps use a liquid, typically water, to create a seal and generate vacuum by the rotation of an impeller within a casing. c. Scroll Pumps: Scroll pumps utilize an involute spiral scroll to compress and trap gas molecules, creating a vacuum. d. Turbo Pumps: Turbo pumps are high-speed pumps that use rotating blades to create a vacuum by transferring gas molecules from one stage to another.
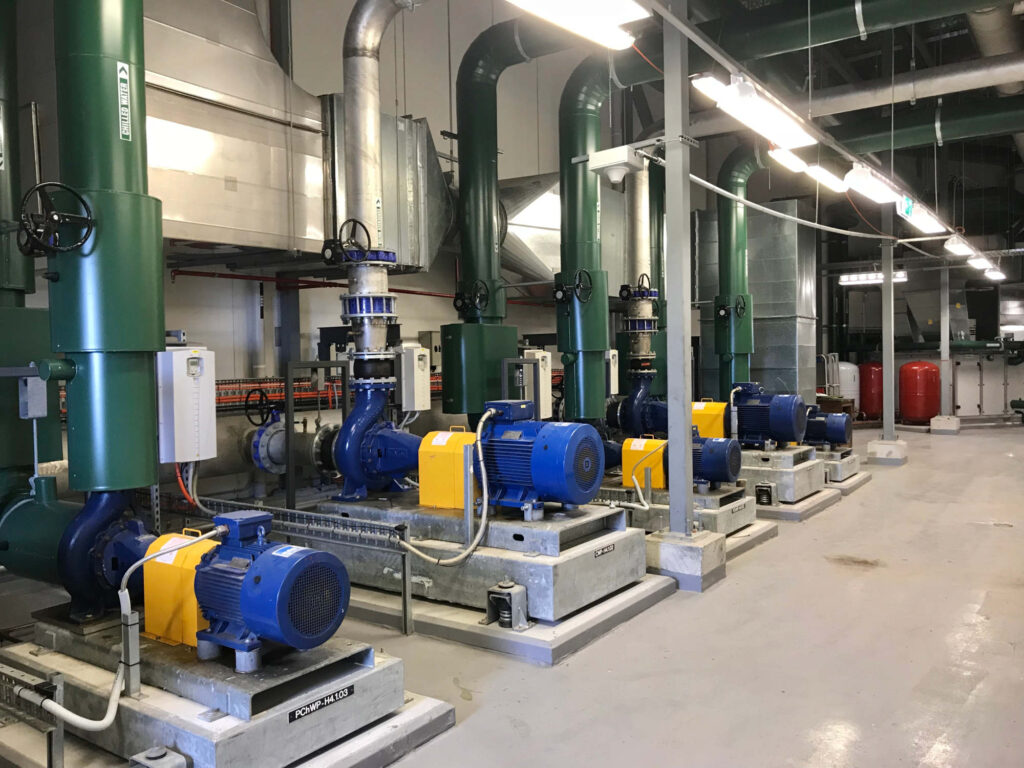
The choice of pump depends on factors such as the nature of the fluid being pumped, flow rate requirements, pressure considerations, and specific industry needs. Pumps play a vital role in industries, ensuring the efficient transportation and distribution of fluids in a wide range of applications.